A Method, background information about the process of ceramics.
I started working with clay about 6 years ago. After years of silk screen printing I was delighted to learn a new technique; a shift from two to three dimensional work. I was hooked immediately and I never stopped working with clay ever since! I continue to learn about the material, the glazing and different techniques every day.
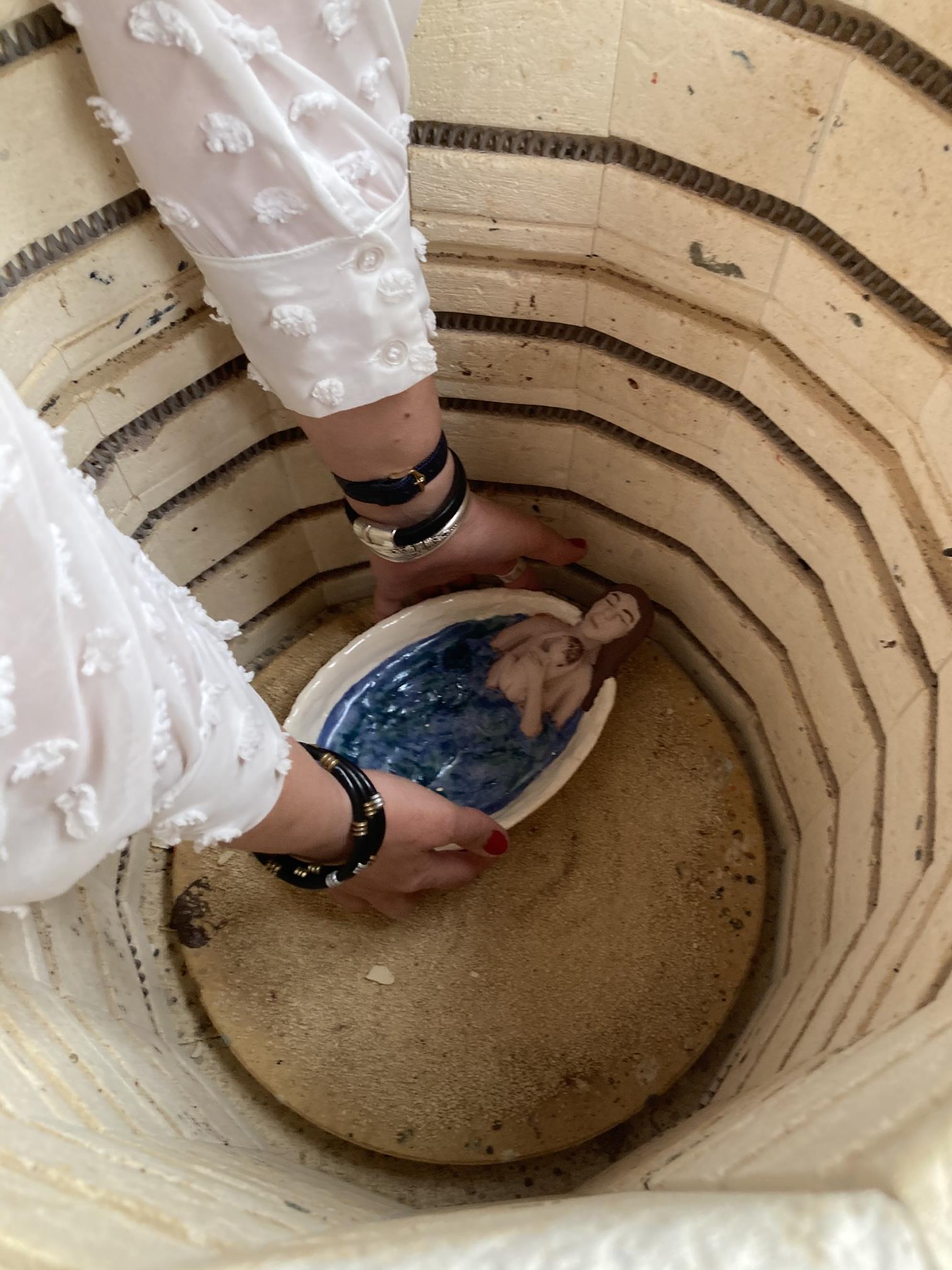
Incredible unpredictable
The process around ceramics is wonderful, but also quite unpredictable. Especially when it comes to working with glazing. Objects never come out the oven the way you imagined them to look like. There are several factors that determine the way an object comes out of the oven. For example the placement (bottom, middle, top or side), which objects you place next to each other (especially when you work with oxides) and the heat of the oven.
When I show people my work they are often surprised about the (long) process from start to finish. So, I thought it might be nice to explain a little about this process.
Earthenware, stoneware and porcelain.
Clay-based pottery can be divided into three main groups: earthenware, stoneware and porcelain. All three can be made in glazed and unglazed varieties, for different purposes. (The first two mentioned use the same type of clay, but different baking temperatures. Porcelain, requires more specific clay materials.) The work I made is earthenware.
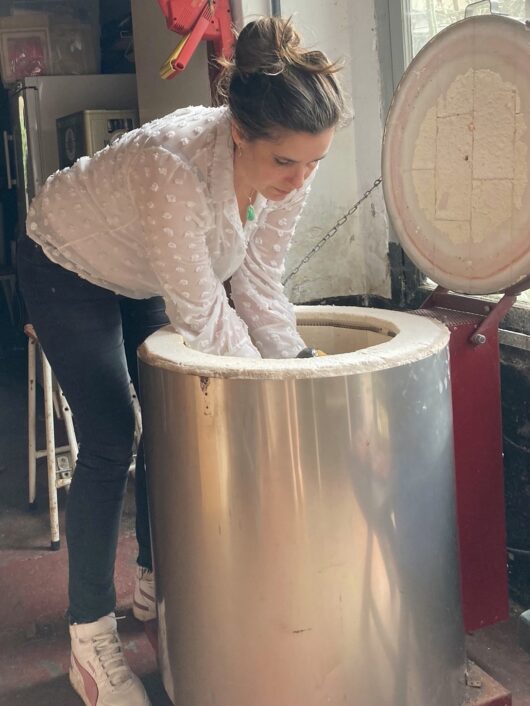
Just keep waiting
After creating an object out of clay, it needs to dry. The drying can take a long time. The water that is in the clay needs to be dried up before the object goes in to the oven. (If not: the remaining water will start to boil and the object will explode. Other objects that are placed next to exploded object can be destroyed too.) Depending on the size, the refinedness and the thickness of the clay this process can take weeks. If an object is “leather-hard” (this means almost dry to the point the clay feels a bit like leather) it can be decorated with “engobe”. (Engobe, from the French word for slip) it is basically a liquid mixture of slurry of clay and/or other materials suspended in water. Engobe can me made (or bought) in many different colours. In comparison to ceramic glaze, it needs to be applied on the clay object before it is baked.
When dried, the object can be baked. This first baking is called “Biscuit fired”. The oven temperature will be between 960C and 1050C. The warming and the cooling down of the oven goes very slowly otherwise the objects will break. This process can take more than 24 hours.
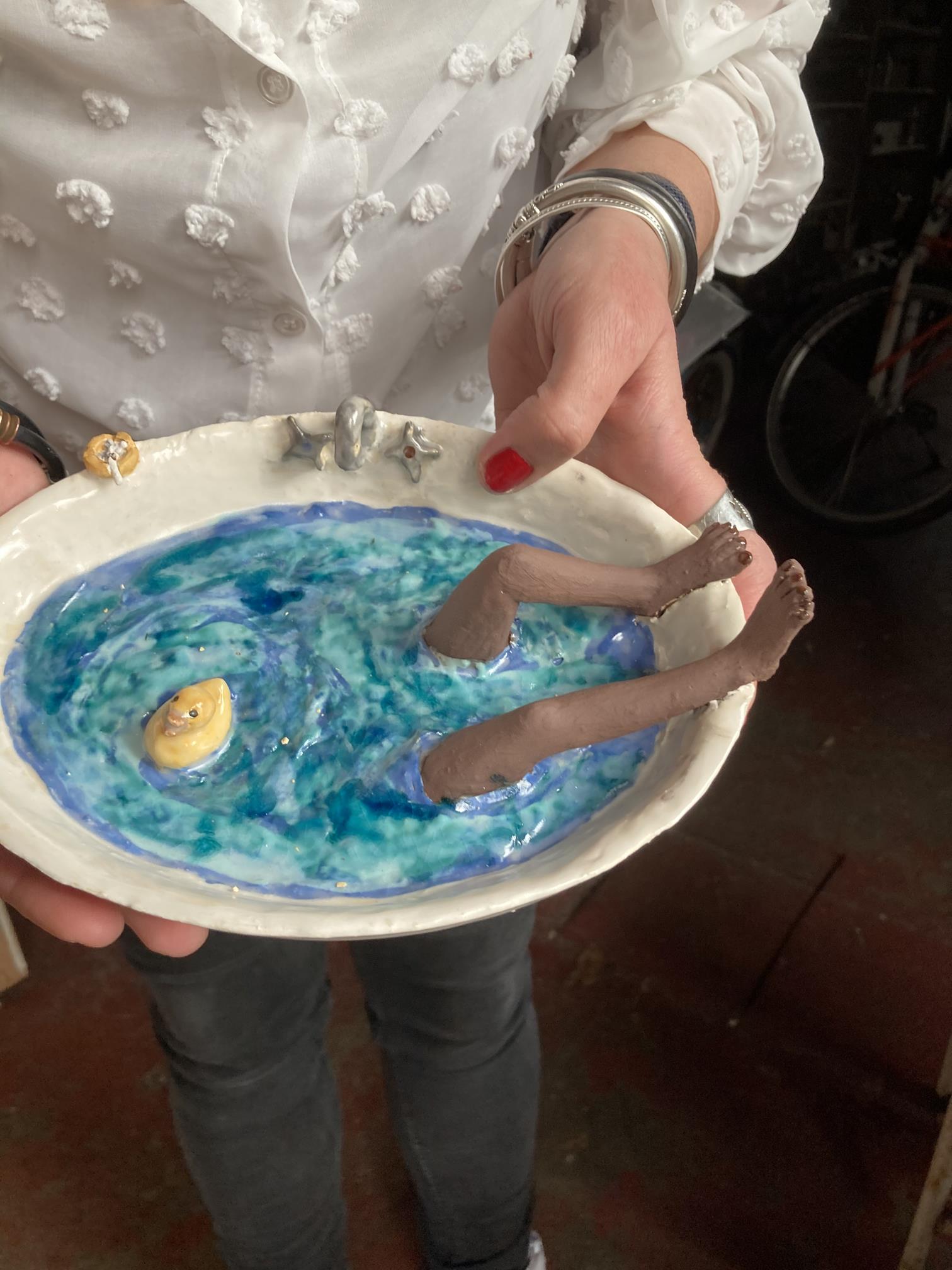
A changing process
The firing changes the clay body in several ways. Mineral components of the clay body will undergo chemical and physical changes that will change the material. After the biscuit fired, the object is much stronger and more solid.
The biscuit baked objects can be glazed. Glaze can serve to color, decorate or waterproof an object. Glazing can be seen as an artform on its own. There are endless varieties of colors and finishes in ceramic glazing. It can take a life time to learn about the different techniques and options. Objects can be painted, sprayed and dipped in glazing.
Earthenware glazed objects are usually baked between 960C and 1180C. The warming and cooling down of the oven goes very slowly to avoid breaking. This process can take up to 24 hours.
Do you want to know more about the process, or do you want to know more about the possibilities of having something made? Please contact me!